I. Overview
The air box pulse bag dust collector combines the advantages of various bag dust collectors with chamber back-blowing and jet pulse cleaning, overcomes the shortcomings of insufficient chamber back-blowing cleaning intensity, and simultaneous jet pulse cleaning and filtering, thus expanding the application range of bag dust collection. Due to the characteristics of the structure of this type of dust collector, the dust collection efficiency is improved and the service life of the filter bag is extended.
This series of products can be widely used in the dust collection systems of cement plants such as crushing, packaging, silo top, clinker cooler and various mills. If used for coal mill dust collection, additional flameproof and explosion-proof measures should be added, and the dust collector structure should also be changed accordingly. It is also suitable for dust collection of gases with extremely high dust concentration. For example, in a grinding system with an O-Sepa powder selector, the dust concentration of the gas is as high as 1000g/m3 (standard) or more. If this series of dust collectors are used for dust collection, a cyclone dust collector can be omitted for primary dust collection. In addition to being used in the cement industry, it is also suitable for dust collection of waste gas from metallurgy, chemical industry, machinery and civil boilers. The filter bag material of this series of dust collectors is generally polyester needle felt, and the continuous use temperature is allowed to be less than 120℃. If the temperature rises, other filter materials should be selected, or cooling measures should be taken before the exhaust gas enters the dust collector.
This series of dust collectors are outdoor and consist of different chambers and different numbers of bags in each chamber, forming a variety of different specifications. The number of bags per chamber is 132, 64, 96 and 128 bags. There are 33 specifications in the whole series, the diameter of the filter bag is 133mm, and the length of the filter bag is 2450mm and 3060mm. This series of dust collectors can operate under negative pressure or positive pressure, and its main structure remains unchanged. Its dust collection efficiency can reach more than 99.9%, and the water content dust concentration of the purified gas is less than 100mg/m3 (standard). The main technical performances of this series of dust collectors are shown in the attached table. If this series of dust collectors are used in cold areas, when the outdoor heating calculation temperature is ≤-25℃, a heating device needs to be added, and the shell of the dust collector also needs to be equipped with an insulation layer.
II. Structure and working principle
This series of dust collectors consists of a shell, ash hopper, ash discharge device, bracket and pulse cleaning system. When the dust-laden gas enters the dust collector from the air inlet, it first hits the oblique partition between the inlet and outlet, and the airflow turns to flow into the ash hopper. At the same time, the airflow speed slows down. Due to the inertia, the coarse dust particles in the gas fall directly into the ash hopper, which plays a role in pre-dust collection. The airflow entering the ash hopper then turns upward and passes through the filter bag with a metal skeleton inside; the dust is captured on the outer surface of the filter bag, and the purified gas enters the clean room above the filter bag chamber and is collected and discharged to the air outlet pipe. The air inlet of the PPC32 dust collector is set on the ash hopper. After the airflow enters the ash hopper, it first hits the baffle at the end of the air inlet pipe, and its function is the same as the above principle. The shell is divided into several independent dust collecting chambers by partitions, and each dust collecting chamber is cleaned in turn at a given time interval. Each dust collecting chamber is equipped with a lifting valve. When cleaning, the lifting valve is closed to cut off the filter airflow passing through the dust collecting chamber. Then the pulse valve is opened to spray high-pressure air into the filter bag to remove the dust on the outer surface of the filter bag. The pulse spray width and cleaning cycle of each dust collecting chamber are automatically and continuously performed by a dedicated cleaning program controller.
III. Characteristics of air box pulse dust collector
The characteristic of the air box pulse cleaning bag dust collector is that it uses chambers to clean in turn, that is, the so-called offline cleaning. When a chamber is sprayed and cleaned, the filter airflow is cut off, avoiding the secondary flying of dust caused by spraying and cleaning. Therefore, the air box pulse bag dust collector can capture gas with dust concentration up to 1000g/m3 (standard).
IIII. Cleaning electrical control device
1. Cleaning control method
The cleaning control method generally adopts the timing method, and the fixed resistance method can also be used. The so-called constant resistance method is to control the pressure difference between the inside and outside of the filter bag. When the differential pressure value of the dust collector reaches the set value (generally 1470Pa), the differential pressure transmitter sends a signal, and the electrical control device is used to clean the dust chamber by chamber according to the prescribed procedure.
2. Function of electrical device
When the multi-chamber dust collector is centrally controlled, a single-chip PLC and sequence controller are used for centralized control. The control has two modes: automatic and manual. When the single-chip microcomputer fails or is under maintenance, it can be switched to manual control at any time. In order to facilitate debugging and equipment maintenance, machine-side control is also provided.
3. The wiring design from the dust cleaning electrical control device to the dust collector inlet terminal is the responsibility of the selector. For the wiring terminals, please refer to the manual of the dust cleaning electrical controller.
V. Composition and supply of dust collector system
1. The dust collector body includes a shell, ash hopper, filter bag device, inlet and outlet pipes, ash discharge device and pulse injection system (including pulse) valve, pipeline, valve, gas source three-piece and gas storage tank, etc. )
2. The dust collector is equipped with an electrical dust cleaning control device, which is generally controlled by timed dust cleaning. If the user requires fixed resistance control, it should be noted when ordering, and the cost of the differential pressure gauge, differential pressure alarm and other instruments controlled by fixed resistance should be calculated separately.
3. The dust collector unloading device is configured according to user needs.
4. The user needs to replace the filter cloth to adapt to other special requirements. If a heating system is required for use in high-cold areas, it can be directly stated when ordering.
5. The dust collector can be shipped as a complete machine or in a disassembled form according to different specifications, and its basic design is the responsibility of the user.
6. The manufacturer provides equipment use and installation instructions for this series of products.
PPCS32, PPCS64 air box pulse bag dust collector technical performance table
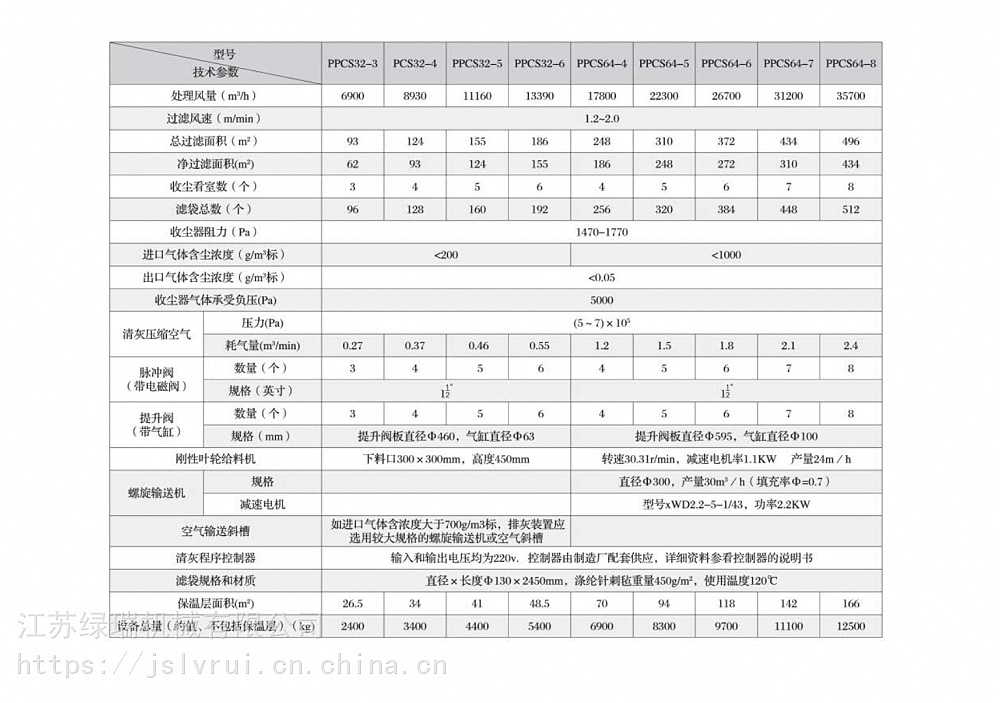
VI. Description
1. The air inlet and outlet can be interchanged, but the inclined partition in the air duct should be installed in reverse, which should be noted when ordering.
2. The ladder can also be arranged at the other end of the dust collector;
3. The ash discharge valve can be installed on the side shown by the imaginary line, but the ash hopper bottom plate and the transmission device of the conveyor should be installed in reverse.
4. The height of the column can be shortened during arrangement, but the height of the column should be noted when ordering.
5. The thickness of the insulation layer is determined by the selector according to different regions. Refer to the insulation layer diagram during construction.